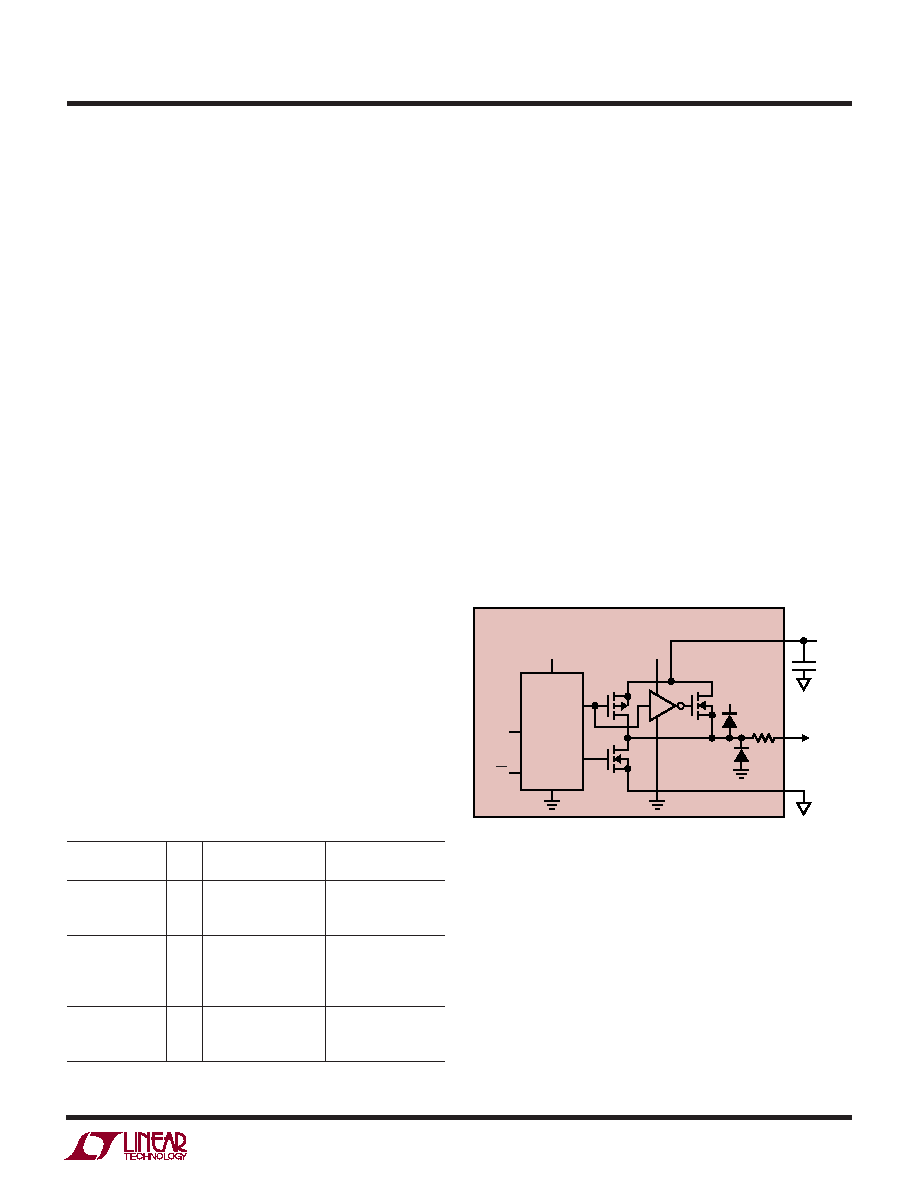
LTC2284
17
2284fa
LTC2284
2284 F14
OVDD
VDD
0.1
F
43
TYPICAL
DATA
OUTPUT
OGND
OVDD
0.5V
TO 3.6V
PREDRIVER
LOGIC
DATA
FROM
LATCH
OE
APPLICATIO S I FOR ATIO
WU
U
Digital Output Buffers
Figure 14 shows an equivalent circuit for a single output
buffer. Each buffer is powered by OVDD and OGND, iso-
lated from the ADC power and ground. The additional
N-channel transistor in the output driver allows operation
down to low voltages. The internal resistor in series with
the output makes the output appear as 50
to external
circuitry and may eliminate the need for external damping
resistors.
As with all high speed/high resolution converters, the
digital output loading can affect the performance. The
digital outputs of the LTC2284 should drive a minimal
capacitive load to avoid possible interaction between the
digital outputs and sensitive input circuitry. For full speed
operation the capacitive load should be kept under 10pF.
Lower OVDD voltages will also help reduce interference
from the digital outputs.
Figure 14. Digital Output Buffer
architecture of this ADC relies on storing analog signals on
small valued capacitors. Junction leakage will discharge
the capacitors. The specified minimum operating fre-
quency for the LTC2284 is 1Msps.
Clock Duty Cycle Stabilizer
An optional clock duty cycle stabilizer circuit ensures high
performance even if the input clock has a non
50% duty cycle. Using the clock duty cycle stabilizer is
recommended for most applications. To use the clock
duty cycle stabilizer, the MODE pin should be connected to
1/3VDD or 2/3VDD using external resistors.
This circuit uses the rising edge of the CLK pin to sample
the analog input. The falling edge of CLK is ignored and
the internal falling edge is generated by a phase-locked
loop. The input clock duty cycle can vary from 40% to 60%
and the clock duty cycle stabilizer will maintain a constant
50% internal duty cycle. If the clock is turned off for a
long period of time, the duty cycle stabilizer circuit will
require a hundred clock cycles for the PLL to lock onto the
input clock.
For applications where the sample rate needs to be changed
quickly, the clock duty cycle stabilizer can be disabled. If
the duty cycle stabilizer is disabled, care should be taken
to make the sampling clock have a 50% (
±5%) duty cycle.
DIGITAL OUTPUTS
Table 1 shows the relationship between the analog input
voltage, the digital data bits, and the overflow bit.
Table 1. Output Codes vs Input Voltage
AIN
+ – AIN–
D13 – D0
(2V Range)
OF
(Offset Binary)
(2’s Complement)
>+1.000000V
1
11 1111 1111 1111
01 1111 1111 1111
+0.999878V
0
11 1111 1111 1111
01 1111 1111 1111
+0.999756V
0
11 1111 1111 1110
01 1111 1111 1110
+0.000122V
0
10 0000 0000 0001
00 0000 0000 0001
0.000000V
0
10 0000 0000 0000
00 0000 0000 0000
–0.000122V
0
01 1111 1111 1111
11 1111 1111 1111
–0.000244V
0
01 1111 1111 1110
11 1111 1111 1110
–0.999878V
0
00 0000 0000 0001
10 0000 0000 0001
–1.000000V
0
00 0000 0000 0000
10 0000 0000 0000
<–1.000000V
1
00 0000 0000 0000
10 0000 0000 0000